In order for a business to flourish, it must achieve supply chain optimization. This means the various functions of the physical supply chain must work together seamlessly, from raw materials to the manufacturers, from warehousing and delivery all the way to the end consumer. In order to make this happen, supply chain information flows between different functions must be automated using supply chain integration
Supply chain integration is often defined as shared information systems that different parties within the supply chain use directly via shared information sources or by integrating with the main information system from the their own applications using standards like EDIFACT and technologies like AS2 – both of which lack flexibility and quick adoption rates. As a result, this integration model is very rigid, and changes to the supply chain may require large-scale changes to the integration architecture.
Rigid integration models may work in supply chains that are fixed and managed internally, and where there are no external drivers – political or economic - causing pressure to change.
However, the closer to the consumer end of the supply chain we get the more flexible supply chain integration typically needs to be. Businesses need to have more and more elasticity in terms of, for example, end-product logistics and supporting services. Nowadays this is often achieved thru outsourcing pieces of the supply chain. Also regulatory requirements, like recent Verified Gross Mass (VGM) in ocean logistics for example, force change on supply chain and thereby to the integration coordinating information flows within. In environment such as this, supply chain integration must be elastic to allow parts of the supply chain to be outsourced or new functions to be introduced quickly.
For example, when companies outsource, they are actually outsourcing pieces of their supply chain to subcontracting organizations that can better and more cost-effectively perform activities. The same subcontractor may be running the same outsourcing functions to multiple customers, and quite seldom the outsourcer has the leverage to force the subcontractor to operate according to its own integration, but instead is faced with the fact that it needs to adapt to the technical requirements – namely interfaces – set by the subcontractor in order to invoke outsourced functions and receive feedback.
Subcontractors provide their technical interfaces in a form of modern REST APIs or Web Services and support JSON and XML based. Meanwhile, your internal systems may still rely on EDFICAT. This means that your integrated supply chain must support both, modern message-based as well as legacy and batch type technologies. Integrations must also enable new integrations to be embedded as part of overall architecture quickly, as new subcontracts are on-boarded, or old ones removed, without causing too much changes to the already existing functionalities.
It is not an easy task to implement flexible integrations that automate data flows between different functions of the supply chain, while simultaneously collecting data from those functions to provide full supply chain visibility over the entire chain.
To summarize things, and add a bit technical twist to this blog post, here are 5 critical rules of supply chain integration that should be considered when implementing it:
1. You need people who understand the business domain and processes. Granted, this is pretty much the requirement in all integration development, not just supply chain.
2. The integration must be built using integration platforms that support modern and legacy technologies.
3. The architecture of integration must support functional scalability allowing the integrated supply chain to be enhanced with new functionalities with minimal effects to already existing integration. SOA (Service Oriented Architecture) and its Composite/Component service model provide a good starting point for the design of the integration architecture.
4. The technical platform of the integration must support automatic load scalability which allows it to automatically scale up and scale for the duration of demand peaks. Your supply chain cannot afford to slow down due to performance issues in the integration.
5. A integration platform must be capable of providing supply chain visibility on a tactical level; highlight errors and bottlenecks in the supply chain, generate proactive alarms when things are starting to look bad or when something is not happening when it should, etc. In addition, it must also make it possible to collect reporting data from different functions of the supply chain and provide that data to the Business Intelligence solution for strategic level reporting.
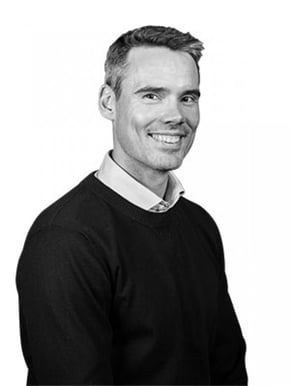